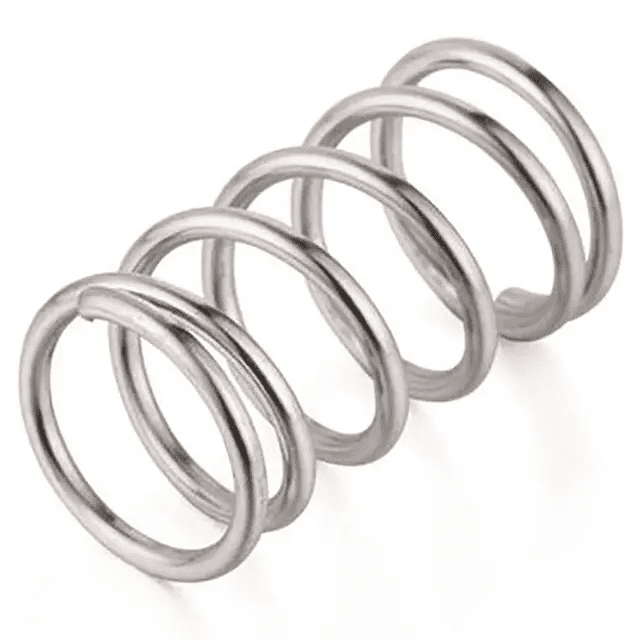
Fatigue And Creep Are Two Different Phenomena That Can Affect The Performance And Lifespan Of Compression Springs. While Both Involve The Deformation Of Materials Under Load, They Occur Under Different Conditions And Have Distinct Characteristics. In This Response, We Will Discuss The Difference Between Fatigue And Creep Of Compression Springs.
Fatigue Is The Progressive And Localized Structural Damage That Occurs When A Material Is Subjected To Repeated Loading And Unloading Cycles. It Is Particularly Relevant In Applications Where Compression Springs Are Subjected To Dynamic Or Cyclic Loading. Fatigue Failure Typically Occurs At Stress Levels Below The Material’S Ultimate Strength, Making It A Significant Concern For The Design And Durability Of Compression Springs.
When A Compression Spring Is Subjected To Cyclic Loading, Such As Being Compressed And Released Repeatedly, It Experiences Stress Variations That Can Lead To Fatigue Failure. The Repeated Loading Causes Microscopic Cracks To Initiate And Propagate Within The Material, Eventually Resulting In Failure. These Cracks Typically Initiate At Stress Concentrations, Such As Surface Defects Or Notches, And Grow Over Time Until They Reach A Critical Size, Causing The Spring To Fail.
The Fatigue Life Of A Compression Spring Is Influenced By Various Factors, Including The Magnitude And Frequency Of The Applied Load, The Material Properties, The Design Of The Spring, And The Surface Condition. To Mitigate Fatigue Failure, Engineers Employ Various Techniques Such As Selecting Materials With High Fatigue Strength, Optimizing The Design To Minimize Stress Concentrations, And Applying Surface Treatments To Improve The Resistance To Crack Initiation And Propagation.
Creep, On The Other Hand, Is The Time-Dependent Deformation That Occurs When A Material Is Subjected To A Constant Load Or Stress Over An Extended Period. Unlike Fatigue, Creep Is Not Associated With Cyclic Loading But Rather With Sustained Stress Levels. It Is Particularly Relevant In Applications Where Compression Springs Are Subjected To Long-Term Static Loading.
When A Compression Spring Is Subjected To A Constant Load, The Material Gradually Deforms Over Time Due To Creep. This Deformation Is Typically Observed As A Slow And Continuous Elongation Of The Spring. Creep Is Influenced By Factors Such As Temperature, Stress Level, And The Material’S Creep Resistance. Higher Temperatures And Higher Stress Levels Generally Accelerate The Rate Of Creep Deformation.
Creep Deformation Occurs Due To The Movement Of Atoms Or Molecules Within The Material, Which Leads To The Rearrangement Of The Material’S Internal Structure. This Rearrangement Causes The Material To Gradually Elongate Under The Sustained Load. The Rate Of Creep Deformation Is Typically Described By A Creep Curve, Which Shows The Relationship Between The Applied Stress And The Resulting Strain Over Time.
To Mitigate Creep Deformation In Compression Springs, Engineers Consider Factors Such As The Material’S Creep Resistance, The Operating Temperature, And The Applied Stress Level. Materials With High Creep Resistance, Such As Certain Alloys Or Heat-Treated Steels, Are Often Selected For Applications Where Creep Is A Concern. Additionally, Reducing The Stress Level Or Operating At Lower Temperatures Can Help Minimize The Rate Of Creep Deformation.
In Summary, Fatigue And Creep Are Two Distinct Phenomena That Can Affect The Performance And Lifespan Of Compression Springs. Fatigue Occurs When A Spring Is Subjected To Cyclic Loading, Leading To Progressive Structural Damage And Eventual Failure. Creep, On The Other Hand, Occurs When A Spring Is Subjected To Sustained Stress Over Time, Resulting In Time-Dependent Deformation. Understanding The Differences Between Fatigue And Creep Is Crucial For Designing Compression Springs That Can Withstand The Intended Loading Conditions And Have A Long Service Life.
I Wish Everyone Can Find Their Own Hardware Accessories, Xiamen Hongsheng Spring Welcome Your Choice!