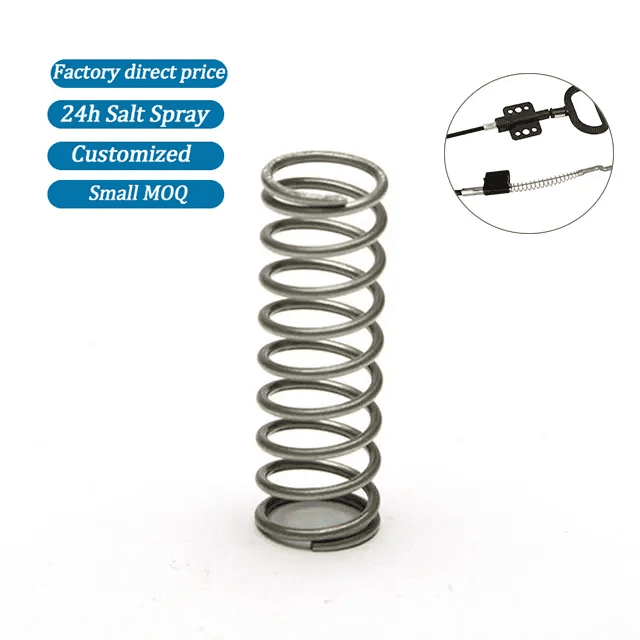
What Is The Difference Between Shot Peening And Shot Peen Flame Turning In Compression Springs?
Shot Peening And Shot Peening Flame Steering Are Two Variations Of The Shot Peening Process Used In The Treatment Of Compression Springs. While Both Techniques Share Similarities In Terms Of Their Basic Principles, They Differ In Terms Of Their Mechanisms, Applications, And Outcomes.
Shot Peening Is A Mechanical Surface Treatment Method That Involves Bombarding The Surface Of A Compression Spring With Small Spherical Particles, Typically Made Of Steel Or Ceramic, At High Velocities.
The Impact Of These Particles Induces Plastic Deformation On The Surface, Creating Compressive Residual Stresses. This Process Helps To Improve The Fatigue Life, Strength, And Resistance To Stress Corrosion Cracking Of The Spring.
Shot Peening Flame Steering, Also Known As Flame Peening Or Flame Spraying, Is A Variation Of Shot Peening That Incorporates The Use Of A Flame Or Torch In Addition To The Shot Particles.
In This Technique, A Flame Is Directed Towards The Surface Of The Compression Spring While The Shot Particles Are Simultaneously Propelled Onto The Surface.
The Flame Serves Two Main Purposes: Preheating The Surface And Enhancing The Plastic Deformation Of The Material.
The Preheating Aspect Of Shot Peening Flame Steering Is Crucial As It Helps To Raise The Temperature Of The Spring’S Surface. This Preheating Step Is Typically Performed To A Specific Temperature Range, Which Can Vary Depending On The Material And Desired Outcome.
By Preheating The Surface, The Material Becomes More Malleable, Allowing For Increased Plastic Deformation During The Shot Peening Process.
The Shot Particles Used In Shot Peening Flame Steering Are Similar To Those Used In Traditional Shot Peening. They Are Propelled Onto The Preheated Surface With The Help Of Compressed Air Or Centrifugal Force.
The Particles Strike The Surface, Inducing Localized Plastic Deformation And Creating A Layer Of Compressive Stress. The Combination Of The Flame And Shot Particles Enhances The Plastic Deformation And The Depth Of The Compressive Residual Stresses.
The Effectiveness Of Shot Peening Flame Steering Depends On Various Factors, Including The Material Of The Spring, The Size And Shape Of The Particles, The Intensity And Coverage Of The Peening, The Temperature Range, And The Desired Outcome.
By Carefully Controlling These Parameters, Manufacturers Can Tailor The Shot Peening Flame Steering Process To Achieve Specific Results.
The Main Advantage Of Shot Peening Flame Steering Over Traditional Shot Peening Is The Enhanced Plastic Deformation And Depth Of Compressive Residual Stresses Achieved Due To The Preheating Step.
This Can Result In Improved Fatigue Life, Strength, And Resistance To Stress Corrosion Cracking Of The Compression Spring. Additionally, The Preheating Step Can Also Help In Stress Relief And The Removal Of Residual Stresses From The Spring.
It Is Important To Note That Shot Peening Flame Steering Is A More Specialized And Complex Process Compared To Traditional Shot Peening. It Requires Additional Equipment, Such As A Flame Or Torch, And Careful Control Of The Preheating Temperature.
Therefore, Shot Peening Flame Steering Is Typically Employed In Applications Where The Benefits Of Enhanced Plastic Deformation And Deeper Compressive Residual Stresses Are Critical, Such As In High-Performance Or Heavy-Duty Compression Springs.
In Summary, Shot Peening And Shot Peening Flame Steering Are Two Variations Of The Shot Peening Process Used In The Treatment Of Compression Springs.
While Shot Peening Involves Bombarding The Spring’S Surface With Shot Particles To Induce Compressive Residual Stresses, Shot Peening Flame Steering Incorporates The Use Of A Flame Or Torch To Preheat The Surface, Enhancing Plastic Deformation And Achieving Deeper Compressive Residual Stresses.
Shot Peening Flame Steering Is A More Specialized Process That Offers Enhanced Benefits In Terms Of Fatigue Life, Strength, And Resistance To Stress Corrosion Cracking, Making It Suitable For Specific Applications Where These Properties Are Crucial.
I Wish Everyone Can Find Their Own Hardware Accessories, Xiamen Hongsheng Spring Welcome Your Choice!