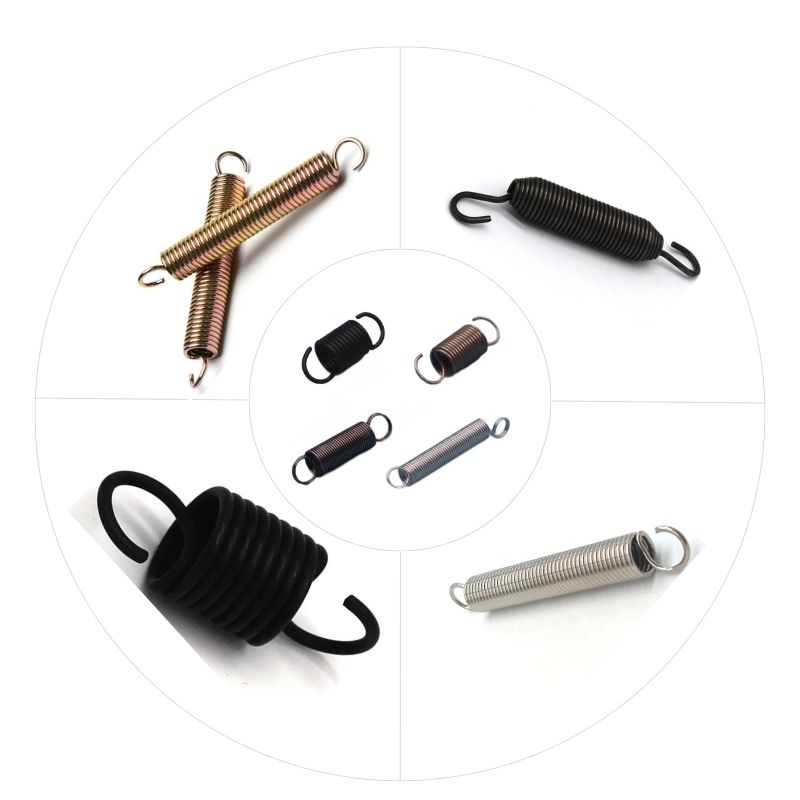
What Are The Disadvantages Ofwhile Tension Springs Offer Numerous Advantages, There Are A Few Disadvantages To Consider As Well. It’S Important To Evaluate These Factors When Determining Whether Tension Springs Are The Right Choice For A Specific Application.
One Potential Disadvantage Of Tension Springs Is Their Susceptibility To Overstretching Or Permanent Deformation. If A Tension Spring Is Stretched Beyond Its Elastic Limit, It May Not Return To Its Original Shape And Lose Its Functionality. This Can Occur Due To Excessive Force, Improper Handling, Or Exposure To Extreme Temperatures. Therefore, It Is Crucial To Carefully Calculate The Required Spring Force And Ensure That The Spring Is Not Subjected To Forces Beyond Its Capacity.
Another Disadvantage Is The Potential For Fatigue Failure. Tension Springs Are Often Subjected To Repeated Cycles Of Stretching And Releasing, Which Can Lead To Fatigue Over Time. Fatigue Failure Occurs When The Spring Material Weakens And Eventually Breaks Due To The Accumulation Of Stress Cycles. To Mitigate This Risk, It Is Important To Select A High-Quality Spring Material And Design The Spring With Appropriate Stress Relief Features, Such As Chamfers Or Radii, To Distribute Stress More Evenly.
Tension Springs Can Also Be Challenging To Install And Replace In Certain Applications. Depending On The Design And Location, Installing Or Replacing A Tension Spring May Require Disassembling Or Adjusting Other Components. This Can Be Time-Consuming And May Require Specialized Tools Or Expertise. Therefore, It Is Important To Consider The Accessibility And Ease Of Maintenance When Incorporating Tension Springs Into A Design.
Another Potential Disadvantage Is The Possibility Of Resonance Or Vibration Issues. Tension Springs Can Exhibit Natural Frequencies, And If These Frequencies Align With The Operating Frequency Of The System, It Can Lead To Resonance. Resonance Can Cause Excessive Vibrations, Noise, And Even Structural Damage. To Mitigate This, Engineers May Need To Incorporate Damping Mechanisms Or Adjust The Spring Design To Avoid Resonance Frequencies.
Additionally, Tension Springs May Experience Issues Related To Corrosion And Environmental Factors. Depending On The Application And Operating Conditions, Tension Springs May Be Exposed To Moisture, Chemicals, Or Extreme Temperatures. These Factors Can Lead To Corrosion, Which Can Weaken The Spring Material And Reduce Its Lifespan. It Is Important To Select A Suitable Material Or Apply Protective Coatings To Enhance The Spring’S Resistance To Corrosion And Environmental Factors.
Lastly, Tension Springs May Not Be Suitable For Applications That Require Precise Force Control Or Where A Constant Force Is Necessary Throughout The Entire Deflection Range. While Tension Springs Can Provide A Relatively Constant Force Over A Certain Range, Their Force Characteristics Can Vary Depending On The Deflection. In Applications Where Precise Force Control Is Critical, Alternative Spring Types, Such As Compression Springs Or Gas Springs, May Be More Suitable.
In Summary, Tension Springs Have Several Disadvantages To Consider. These Include The Potential For Overstretching Or Permanent Deformation, Fatigue Failure Over Time, Installation And Replacement Challenges, Resonance And Vibration Issues, Susceptibility To Corrosion, And Limitations In Precise Force Control. By Carefully Evaluating These Factors And Considering The Specific Requirements Of The Application, Engineers Can Make Informed Decisions About Whether Tension Springs Are The Appropriate Choice Or If Alternative Spring Types Should Be Considered.
I Wish Everyone Can Find Their Own Hardware Accessories, Xiamen Hongsheng Spring Welcome Your Choice! Using Tension Springs?